We've tried to ensure the information displayed here is as accurate as possible. Should there be any inaccuracies, we would be grateful if you could let us know at info@ipohworld.org . All images and content are copyright.
(Please click on the thumbnail for a bigger image.)
Choong Kee Foundry Cast Machinery Parts For The Local Mines - Part 1

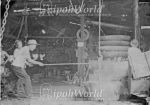
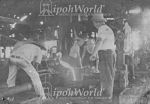
Choong Kee Foundry was once a prolific manufacturer of replacement machinery parts and other items for the local mining industry. The owner, Mr Choong Kee, was an industrious person who set up the foundry by buying and modifying a boiler from a scrapped ship in Singapore (which he took out of the ship himself and transported to Kampar) and with considerable ingenuity, turned it into his blast furnace at a fraction of the cost of purchasing a ready made furnace.
To manufacture cast iron parts, the blast furnace is fed with scrap iron, pig iron and coke, with a continuous blast of air to ensure the melting process.
Also required are specialist moulds, made from engineeringly precise patterns. The moulds themselves are made of sand mixed with clay and carbon powder. The inner surface of the mould is then coated with a layer of graphite to prevent the molten iron adhering to the sand mould.
Once the iron is fully melted and the moulds ready for casting, clay lined ladles are filled with molten iron from the furnace. Different sized ladles are used according to the size of the items being cast. When the ladle contains sufficient material, a clay plug is fitted into the tapping hole of the blast furnace to stop the flow. At the same time, slag is skimmed off the surface of the metal in the ladle and a layer of fine sand is sprinkled on to the surface of the molten metal to act as a cover. The molten metal is then poured into the waiting moulds and when cooled the moulds are broken open to reveal the new cast iron part which, depending on what it is, will require finishing before despatch.
From left to right the photographs show: