We've tried to ensure the information displayed here is as accurate as possible. Should there be any inaccuracies, we would be grateful if you could let us know at info@ipohworld.org . All images and content are copyright.
(Please click on the thumbnail for a bigger image.)
A Bucket Dredge In Kampung Gajah
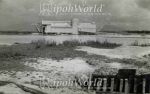
The picture shows one of the many bucket tin dredges that operated in man-made pools throughout the Kinta Valley before the collapse of the tin price made operating these monsters completely uneconomic.
Dredges cut away one wall of the pool and dump the waste sand (known as tailings) against the opposite wall. They were usually floating in an artificial pool and worked best in swampy land. The introduction of dredging had a greater impact on Kinta than anywhere else in the Federated Malay States (FMS).
An early attempt (in 1906) by Osborne and Chappel to employ a Suction Dredge for tin mining was unsuccessful.
The first successful bucket dredge that operated in Malaya was introduced by Malayan Tin Dredging Ltd., in January 1913. This dredge featured 150-foot hull with ten cubic foot buckets connected together in what was called the bucket 'ladder'. The dredge was steam-powered and could dig to a depth of 50 feet. The company was so successful that a village grew up called Kampung MTD close to their Batu Gajah tin fields, and the village inhabitants formed the bulk of the labour force.
The lip of each dredge bucket cut deep into the ground below the dredge and carried a chunk of ore-bearing material high up into the dredge. When the bucket turned over at the top of the ladder to move downwards, the material dropped into the 'drop-chute' for the next stage of operation. The buckets continued their journey along the endless chain to dig up another load. These buckets were very expensive, costing 100 pounds sterling per piece in the 1920s. Although dredges and buckets became larger and more modernised and were often powered by electricity the basics of this first dredge remained unchanged.
From the buckets the ore bearing material would pass through a number of operations to remove the valuable ore from the sand and soil. First the soil was washed with high pressure hoses, freeing the ore which passed through a revolving screen with the water where it was collected in a tank underneath the screen.
Next the ore and water flowed along distribution chutes to pulsating jigs which alternately pumped water through holes in the jigs and then sucked it back. This further separated the ore from the waste soil and pebbles and allowed it to flow into the sump below, the remaining waste was carried away to the rear and off the dredge to become what is known as tailings.
Secondary jigs were then employed to further purify the ore before it was passed into rubber buckets ready for transportation off the dredge for further treatment and concentration. Pure Tin Oxide (the ore), scientifically called Cassiterite contains over 75% metallic tin.
Before the introduction of the more technical machinery like revolving screens and jigs etc, the processing of the tin inside the dredge was more akin to the basic open-cast mining Palong, where the tin bearing soil was washed along bays with riffles acros them, the latter catching the tin. These were known as 'Tin Tables'.
Although the hard excavating work, previously undertaken by hand, was now done by the dredge, running a tin dredge 23 hours a day and 7 days a week still required a lot of skilled and unskilled workers working in shifts. The 24th hour in every day was used to grease and maintain those parts of the machinery which could not be accessed when the dredge was operating.
In 1914 there were 3 dredges in Malaya and in 1915 there were 11; by 1920 the total had risen to 20 and by 1931 to 30. The greatest number of tin dredges ever operating at one time in Malaya was in 1929 when there were 105 and not a single dredge was idle.
In 1940, 104 dredges were operating across Malaya out of a total available of 123, the remaining 19 being stopped. This was the highest number of dredges ever recorded in Malaya.
In 1952, there were 39 dredges operated by 15 companies in Kinta Valley alone. All these dredges were originally built before the war and their capacities ranged from 162,000 to 396,000 cubic yards per month. Seven of the larger units were capable of digging more than 100 feet deep.
In 1965, out of a total of 82 tin dredges available in the country, during the month of July only 70 were operating. The decline in the industry had started!
In 1965 a new dredge cost between 10 and 15 million dollars to build; one such dredge came into operation that year and two more were still being built despite the obviously reducing requirement.
At the same time other dredges were still being rebuilt, the total task being to dismantle into transportable pieces, remove to a new site and rebuild. For a small dredge in 1965 the total cost of such an operation would have been $4 to $5 million.
This information is adapted from publications produced by The Tin Industry (Research and Development) Board.
One other type of dredge, known as the 'Grab Dredge', was in use in Thailand for mining tin from the sea bed.
To see the sequence of Tin Dredging Operations – Step by Step, click here.
To read more about Dredge Bucket Coolie, click here.
To read more about MTD Village, click here.
To read more about Dredge Tin Tables, click here.
To read more about the failed Suction Dredge, click here.
To read more about a Grab Dredge, click here.
To read the book "Mining in Malaya" in e-Book form, click here.